Safe Temporary Power and Lighting Strategies For Refinery Turn-around Activities
Introduction
Periodic shut-down, inspection and maintenance activities (typically referred to as a turnaround) are an essential reality for refineries, and are needed to ensure safe, efficient operation. The scope of the turnaround may vary depending on the processes involved, but even minor activities encompass a wide range of tasks that occur concurrently and must be orchestrated with great care to avoid damage to equipment or danger to personnel.
Personnel are constantly exposed to hazardous conditions; therefore, safety is always of paramount importance. Adherence to safety regulations is mandatory to avoid injury or damage to the facility, environment and surrounding areas. Temporary power and lighting solutions, essential for maintenance activities, must also meet rigorous regulatory and safety standards especially when subjected to environments where vapor and gas are present.
This paper will explore design and regulatory requirements necessary to meet these standards, along with identifying implementation techniques specific to the challenges commonly encountered during a refinery turn-around.
Turn-around Overview
Petroleum refineries carry out the process of splitting crude oil into its component parts, which are then further processed into useful products such as fuels, lubricating oils, greases, petroleum solvents and asphalt. This process exposes equipment to a wide array of caustic liquids and gases thus limiting operational life and mandating the need for scheduled and unscheduled maintenance activities typically referred to as “turnarounds”.
Turnarounds are required to maintain safe and efficient operation and typically target specific operating units; a major turnaround could involve the crude or catalytic cracking units while a minor turnaround could involve the alkylation unit, isomerization unit or sulfur plant. They may also encompass more specific activities such as inspection and testing, debottlenecking projects, revamps and catalyst regeneration projects. The complexity and length of time involved will also vary depending on the process unit and may range from several weeks to many months.
The financial stakes are also high, both in terms of lost production while the process unit is offline and in terms of direct costs required to execute the project such as labor, tools, heavy equipment and materials. These activities typically comprise the most significant portion of a plant’s yearly maintenance budget and can have a direct impact on the company’s bottom line; additionally, the potential for serious injury or death during these activities is always a concern that drives the need for continued emphasis on processes, procedures and the utilization of safe equipment.
Safety is always a primary concern during any refinery operation and it is of even greater significance during a turnaround due to the number of temporary workers involved, the close proximity of construction equipment, and the hazardous environments to which some workers will be exposed. Mandated safety practices are broad in nature encompassing personal safety equipment, procedures for completing specific tasks, awareness of unsafe conditions, as well as requirements for temporary power and lighting solutions that may be required for use in hazardous locations.
Safety Essentials
Refinery personnel are exposed to a wide range of hazardous conditions, and must be aware the proper precautions necessary to avoid personnel injury or damage to the facility, environment and surrounding areas.
Turnarounds involve activities such as welding, drilling, sanding and cutting, all of which require adequate lighting, and all of which require electricity to function. Additionally, there are many times when the electrical distribution, lighting and tools must be capable of operating in different types of hazardous locations.
The National Electric Code (NEC) classifies hazardous locations in three ways by Type, Condition and Nature. The Types of hazardous conditions include gas and vapor, dust, fibers and flyings. To simplify the identification of these conditions they have been categorized as Class I, Class II and Class III respectively.
Two kinds of hazardous conditions are identified by the NEC, namely Division 1 which signifies a normal condition (i.e. normal or regular exposure) and condition 2 which is abnormal (i.e. occasional, infrequent exposure). The Nature of the hazardous substance is further defined as Groups A, B, C, and D in Class I locations, and, in Class II locations: Groups E, F, and G. These groups represent the ignition temperature of the substance, the explosion pressure, and other flammable characteristics.

Chart 1. Hazardous Location Definitions
A quick example will help illustrate how the classification process works; liquid propane (LP) gas is contained in a closed tank and must be classified. LP gas is a Class I substance (gas or vapor) and Division 2 because it would only be in the atmosphere in the event of an accidental rupture or leak. LP is categorized as a Group D material. Group D includes many of the most common flammable substances such as butane, gasoline, natural gas and propane (See Chart 1).
Chart 1 provides a summary of the Class and Division definitions.
All temporary electrical distribution and lighting solutions used in classified hazardous locations must be designed to function in these environments, and are only available from a select group of manufacturers. Safety is the primary concern; therefore, it is no longer an accepted practice for contractors build electrical panels with the hope that catastrophic failure points will be avoided.
Equipment Design Overview
Equipment designed for use in Class I, gas and vapor, environments must be able to contain an explosion from within the device; therefore, one of the key characteristics of these devices is strength. Ignition sources, such as arcs and sparks, may be produced during the normal operation and without proper protection could ignite vapor or gases in a hazardous location atmosphere. Samples of these sources include relay contacts, switches, and motor starters.
Other sources of ignition exist as well and often result from high temperatures produced by equipment such as lamps and fixtures. Again, these devices are a concern if the temperature exceeds the ignition point of flammable atmospheres. There are critical design requirements that are focused on the ability of equipment to withstand an explosion, as well as to limit the escape of flame to the surrounding area.
Class I equipment must have the following characteristics:
- Explosion-proof
- Strength
- Durability
- Capable of withstanding the internal strain of an explosion
- Well Established Flame Path
- Escape path for exploding gases
- Gases are cooled off and flames extinguished
- Several type exist including threaded and ground surface
- Special Fittings and Seals
- Prohibits hot gases from traveling through the conduit system
- Prohibits flammable dusts from entering dust-ignition-proof enclosures
- Prohibits ignition in other areas of the closed system
Equipment must also meet rigorous standards and performance criteria in order to be certified for hazardous location use. Nationally Recognized Testing Laboratories (NRTLs) such as UL and CSA have established test criteria for hazardous location equipment and developed facilities with controlled environmental test capabilities to facilitate certification.
However, maintaining the integrity of all flame paths while in service and throughout the functional life of the equipment is critical. Damaged equipment may provide a path that could allow the release of flaming gases; therefore, regular inspections and care during shipping, handling and storage can greatly reduce this risk.
Proper design and fabrication techniques can also reduce exposure to these risks and the implementation can vary greatly; therefore, it is critical to choose a solution provider with experience and a proven track record in hazardous location equipment design and manufacturing.
Temporary Power Distribution
Facility maintenance and engineering personnel must have adequate power and lighting resources available during turnaround operations or risk costly delays, which is why temporary solutions play such a key role during these activities. Temporary power solutions are comprised of a number of different configurations including transformer-based power distribution, non-transformer power routing, interconnect cabling and cable protection.
Hazardous location temporary power distribution solutions pose new challenges for the manufacturer beyond those seen in traditional Class I applications. The very nature of temporary power infers portability and the need to allocate these resources between multiple work sites reliability, with minimal effort, labor, and down time.
Key characteristics of temporary power solutions for use in petroleum refineries, as well as other hazardous locations, include:

Figure 1. Ericson E-Cart2 XP
- Certified for Use in Classified Areas
- Quick, Simple Connectivity
- Suitable for Outdoor Use
- Support for Easy Relocation and Movement
- Light Weight, Heavy Duty Frame Construction
- GFCI Protection for Equipment and Personnel
Manufacturers, such as Ericson Manufacturing, are leading the way with a new generation of turn-key, explosion proof temporary power solutions ideal for a wide range of hazardous location applications including Class I, Division II. The job-tested E-Cart 2™ XP power distribution solutions (shown below) are built rugged enough to survive the harshest jobsite environments and designed to the meet the latest Safety Certifications and Standards (See Figure 1).
Key characteristics of the E-Cart 2™ XP include:
- UL Listed
- NEMA 3R (outdoor) Rated
- GFCI Circuit Protection
- Front Mounted Main Locking Handle
- Class I, Div. 2, Groups C and D Certified
- Flexible Voltage and Circuits
- Copper-free Cast Aluminum Alloy Panels
- Heavy Duty, Light Weight, Spark Resistant Aluminum Frame
- Electrical Grade Silica Encapsulated and Ventilated Transformers
Designed for use In Class I, Division 2, the factory sealed panelboards are used to control lighting and appliance, power circuits and power distribution in applications requiring branch power distribution, over current, and short circuit protection.
Utilizing electrical components from leading manufacturers, the factory sealed panelboards are pre-wired and factory sealed from the circuit breakers inside the flameproof enclosure to the main distribution blocks and branch terminals housed in an IP66 rated, Type enclosure. The factory seal between the breaker enclosure and terminal enclosure eliminates the need for external sealing.
The E-Cart2 XP is equipped with padlockable external operating handles, copper bus, isolated neutral and ground bar, GFI or EPD breakers, and terminal blocks. Gasketed covers provide type NEMA 4X rated protection for a water tight seal.
Flexible configuration alternatives are essential and must provide the ability to meet unique application requirements without the cost typically associated with a custom solution; minimal setup and teardown time can also be achieved with this approach, saving valuable time and expense. Portability is another important consideration that is driving leading manufacturers to standardize on platforms constructed of heavy-duty welded aluminum; this approach reduces the overall weight of the solution while maintaining exceptional strength and durability characteristics.
Temporary Lighting
Once temporary power has been addressed the next critical element is lighting. Lighting solutions are more commonly designed for Class I, Division 1 operation, and so may be freely used in Division 2 locations. Lighting must adhere to the same stringent requirements as power while supporting various form factors to address different application requirements.

Figure 2. Class I, Div. I Lighting
Essential features recommended for any hazardous location temporary lighting solution include:
- Resistant to breakage from drop or impact
- Wet Location Use
- Lightweight Construction
- Class I, Division 1 Certified
- Resistant to High Temperatures
- Resistant to Chemicals, Acids and Chipping
- Heavy-duty Non-sparking Aluminum Guards
- Non-conductive, High-impact, Reinforced Handle
Maintenance personnel require access to unique areas, and the specific location will dictate the type of light that is needed. For example, explosion proof stringlights are an ideal solution for general access areas and walkways, whereas handlamps are more appropriate for activities such as inspection and close area work.
Hazardous location lighting must be rugged and designed to last, and be readily available in multiple configurations including spot, flood, and stringlight. Certification for wet location use is mandatory, and other features such as aluminum guards, hanging hooks, and rubberized molded “T” junctions with heavy duty hang tabs further enhance the usability of these products (See Figure2).
Cable Management
One final aspect of the temporary power and lighting puzzle involves cable management, both to the power distribution unit and beyond to the individual tools and lamps. Cable damage can pose significant safety risks; therefore, cabling must be adequately shielded from a multitude of worksite hazards to protect against open arcing and sparks.
Extreme duty cable protectors can deliver unmatched security and protection even under the heaviest loads. These devices also ensure security for pedestrian traffic, protection against dangerous trip hazards and electrical shock hazards (See Figure 3).
Key benefits include:

Figure 3. TuffTraxx Cable Management System
- Safe Surface for Pedestrian Traffic
- Hinged Lid for Easy Cable Loading
- Non-conductive Shock Barrier Protection
- Tread Plate Surface for Increased Traction
- Y-Adapters Deliver 45° and 90° Cable Routing
- Rugged, All-weather Polyurethane
- T-style Connector Interlocks
This type of product is typically constructed from light-weight, all-weather polyurethane ideal for delivering functionality such as extended service life, simplified configurability, and quick set-up and tear-down.
Case Study
A major international producer of gasoline and chemical products undertook a multi-billion dollar modernization project to expand crude processing capabilities, as well as improving operational reliability and efficiency. This effort focused on providing greater energy security as conventional supplies of lighter crudes diminish and are replaced by heavier sour crude oil from alternative sources.
The upgrade project included the installation of a new crude distillation unit, a coker, world scale hydro-treating and sulphur recovery, as well as general improvements to the facilities’ infrastructure, all while maintaining safe operations in other areas of the plant (See Figure 4). The ultimate goal of the project was to increase the refinery’s capability for gasoline and diesel production with an aggressive operational target of mid-2012.

Figure 4. Refinery Turn-around
Safety is always of paramount important during any maintenance activity, but it is of even greater concern during this type of operation when more than 8,000 contractors are on-site. Adherence to well defined policies and procedures are an important part of the safety equation; however, utilizing equipment that has been designed to operate safely in hazardous environments is just as critical.
Ericson Manufacturing’s temporary power and lighting solutions were selected based on a number of key performance criteria including:
- Class I, Div. 2 Rated
- System Level Certification
- External Resettable GFCI Breakers
- Rugged Construction
- Light-weight and Mobile
- Price / Delivery
The E-Cart2 XP transformer-based power distribution center was configured to meet the user’s needs within budget, and with the ability to meet an aggressive delivery schedule, thanks to the modular nature of the solution and the ability to easily mix and match product features and options. The scope of the turn-around required the simultaneous deployment of over 45 E-Cart XP units throughout the facility to safely power temporary lighting as well as a wide array of tools.
Summary
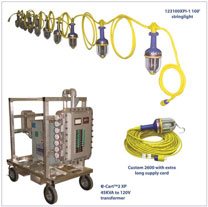
Figure 5. Temporary Power and Lighting
Turnaround activities are inherently dangerous; therefore, management must incorporate a safe well planned execution strategy. Equipment selection is a critical aspect of this strategy and temporary power and lighting solutions, essential for maintenance activities, play a significant role (See Figure 5).
Adherence to regulatory and safety standards, especially when operating in environments where workers are exposed to explosive vapor and gas, must not be overlooked. Vendors should be carefully scrutinized for strict compliance to these standards; additionally, a vendor’s experience designing and serving this application space should also be evaluated.
Accidents can never be completely avoided, but thorough planning, employee training, thoughtful execution and proper equipment selection will greatly increase the likelihood of a safe, successful outcome.
For additional information on industry leading temporary power and lighting solutions designed and certified for hazardous location use contact Ericson Manufacturing Company, 4215 Hamann Parkway Willoughby, Ohio 44094 at (440)951-8000. Email inquiries can be sent to info@ericson.com or visit our website at www.ericson.com
Share on Socials!
Arc Flash & Electrical Safety Training
Dur-A-Lift, Inc. Building New Factory and Offices in Lyon County
The Magic Number
Leaders in Electrical Safety
• Aramark
• Bowtie Engineering
• Enespro
• Ericson
• I-Gard Corporation
• IRISS
• KERMEL, INC.
• Lakeland Industries
• MELTRIC Corporation
• National Safety Apparel
• National Technology Transfer
• Oberon
• Saf-T-Gard
• SEAM Group
Subscribe!
Sign up to receive our industry publications for FREE!